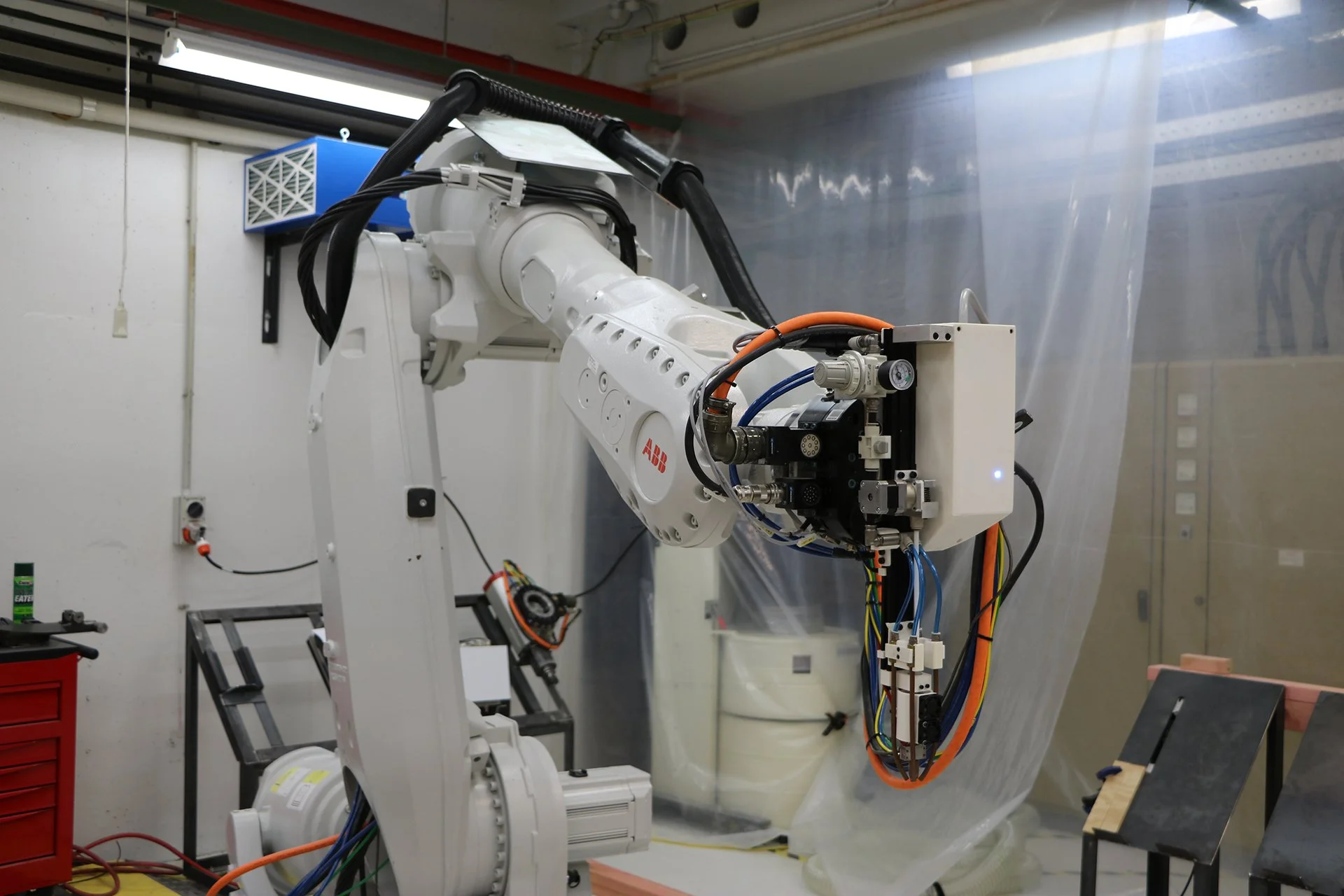
Robotic Spatial Printing for Designers
In 2018 I completed my Masters in Design at Victoria University Architecture and Design School. I was on scholarship from both Callaghan Innovation and Scion with the brief of building a freeform 3D printing platform using the ABB 6-axis robotic arm at VUW that could experiment with various natural fiber reinforced biopolymers created by Scion.
Alongside these physical systems was a design framework for structures using Rhino and Grasshopper, which calculated toolpaths from given inputs and generated either the RAPID code to control the ABB robot and proprietary extrusion system or the GCode for the independant system depending on which was used.
First Extruder
Ultimately I ended up building two different systems to perform freeform printing, the first was a standalone 3D printing attachment that used an existing tool-changer for material deformation and was controlled independantly of the robot, This was intended as a first prototype system so that we could better understand the constraints of freeform printing. We learned a lot from this system, and after dialling in a lot of our variables we found that we needed some greater control and integration with the robot.
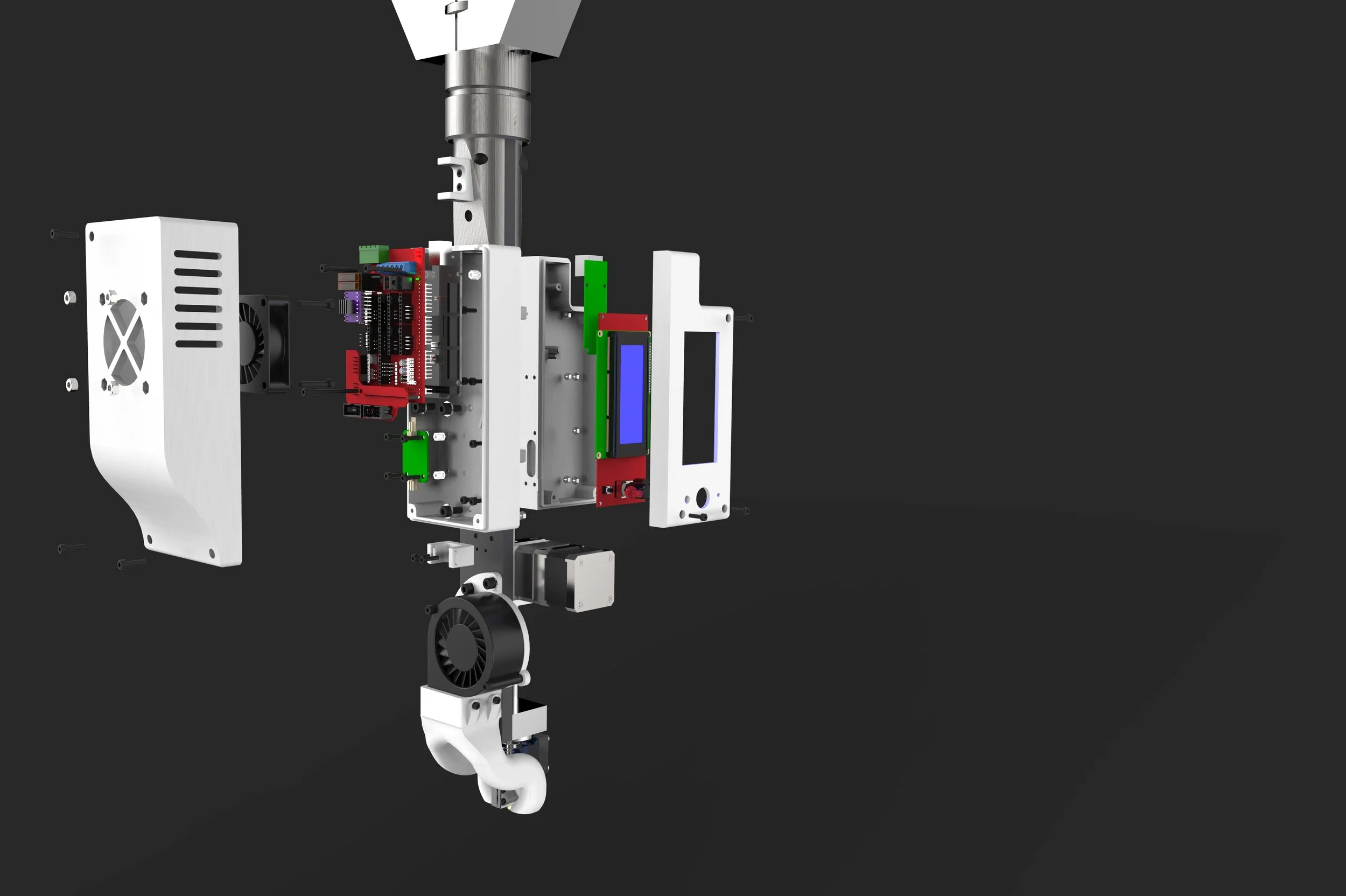
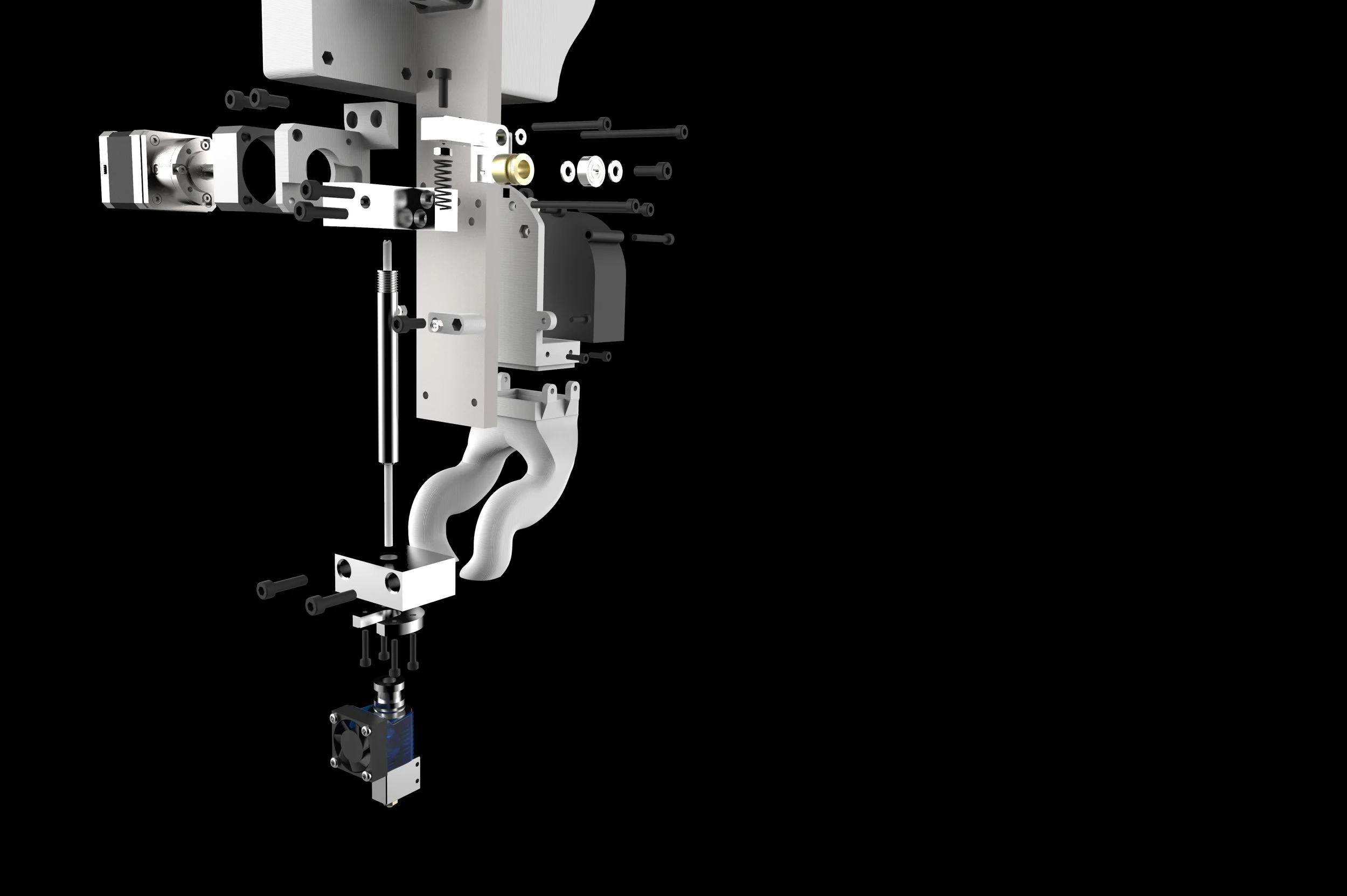
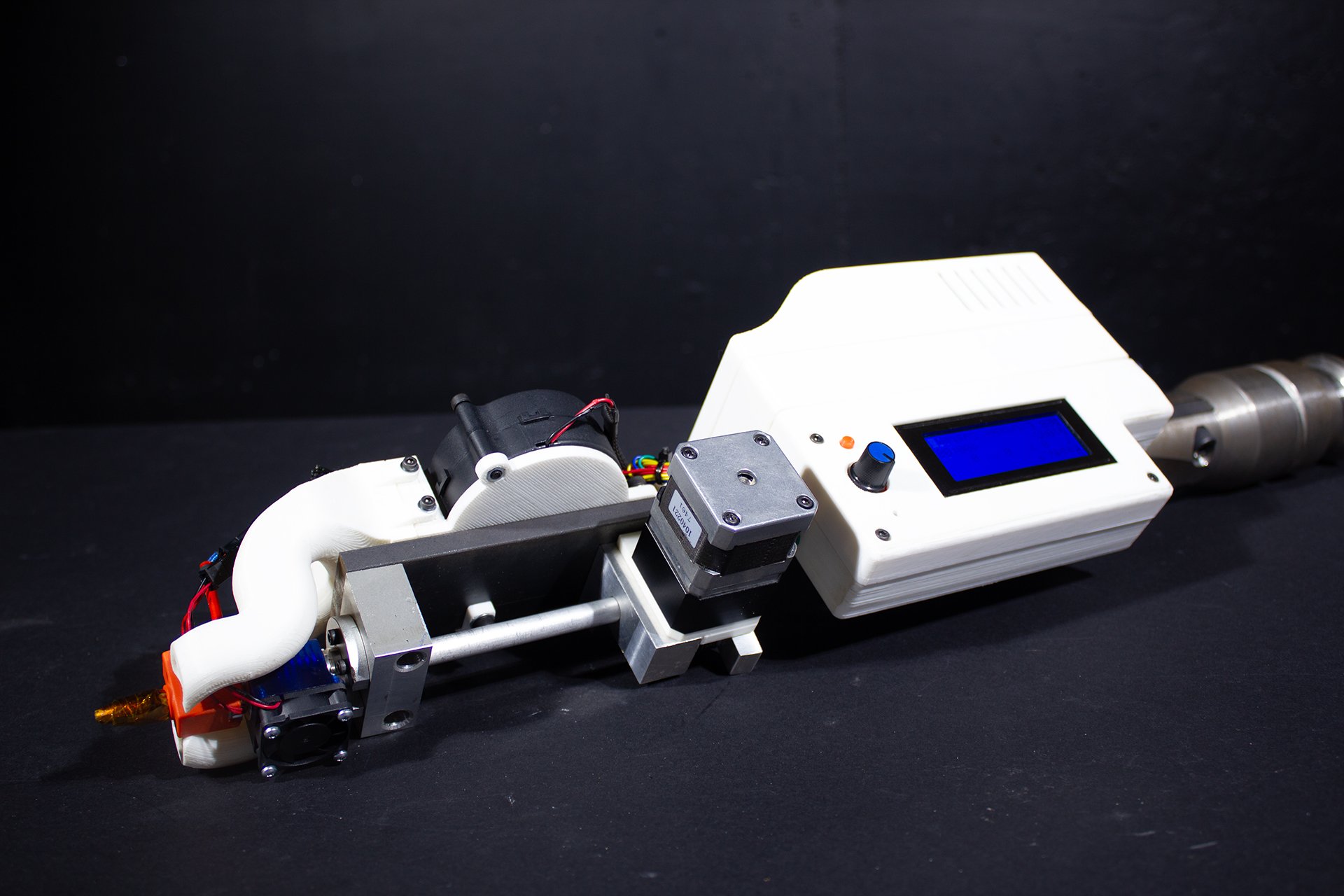
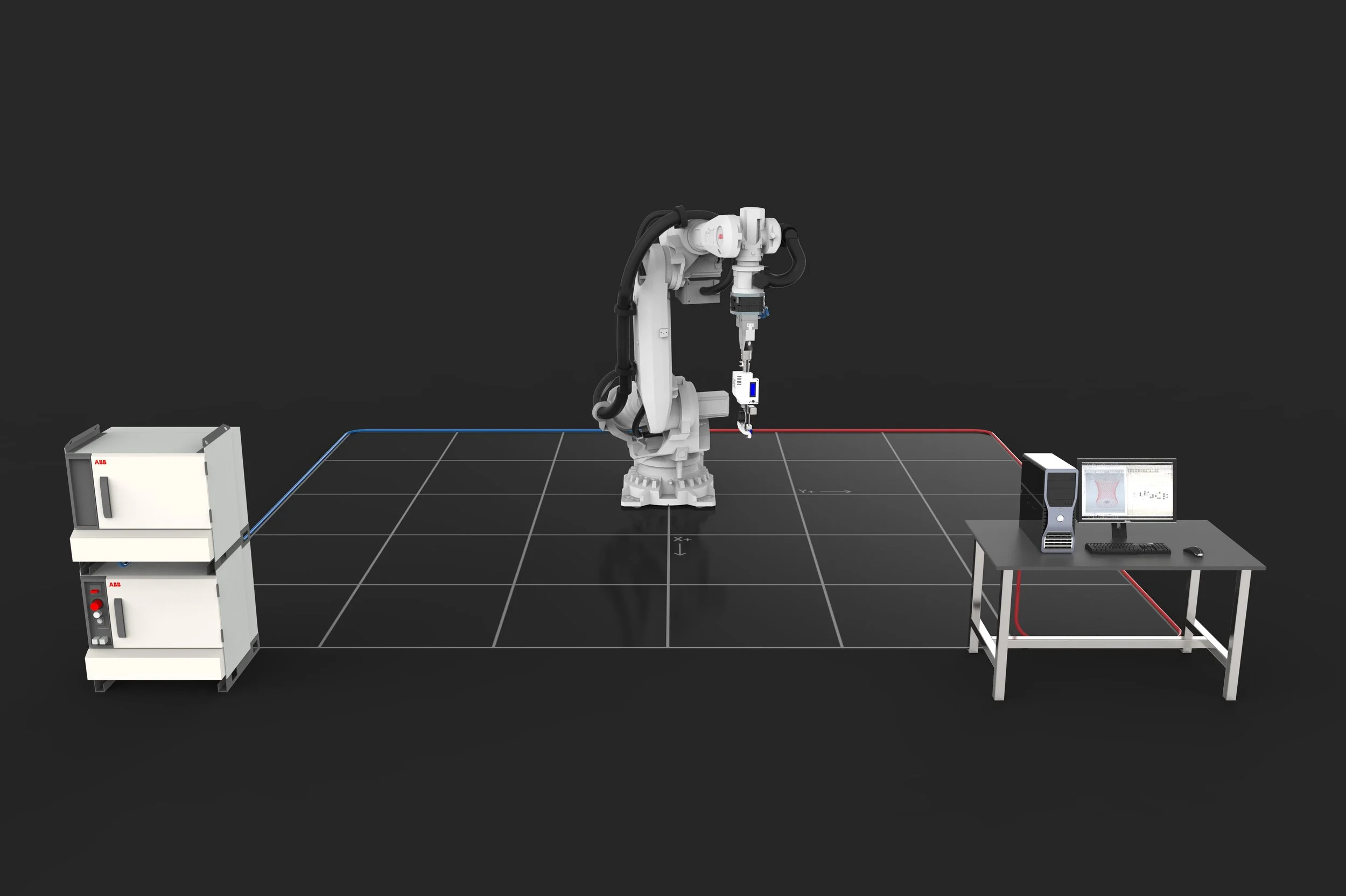
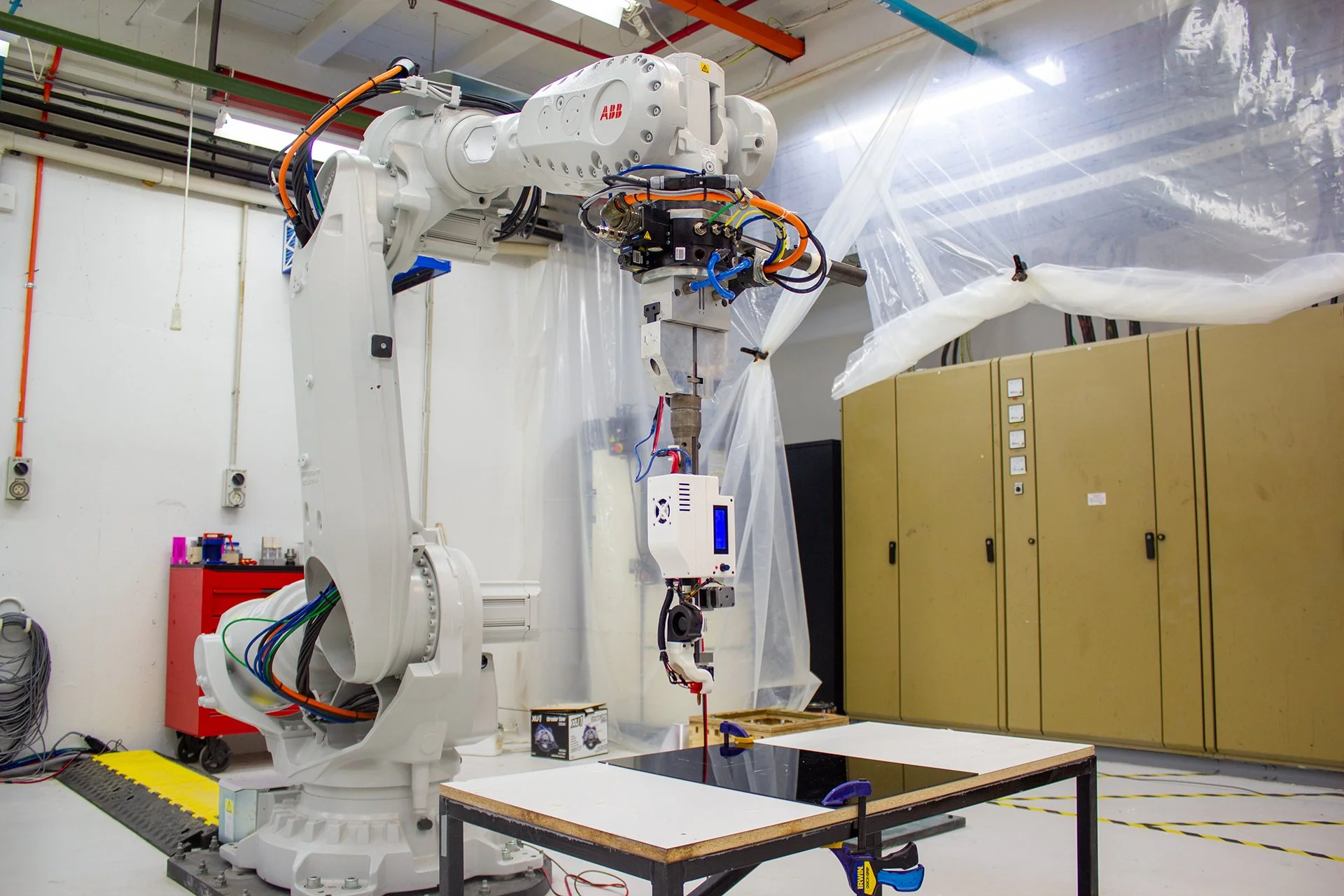
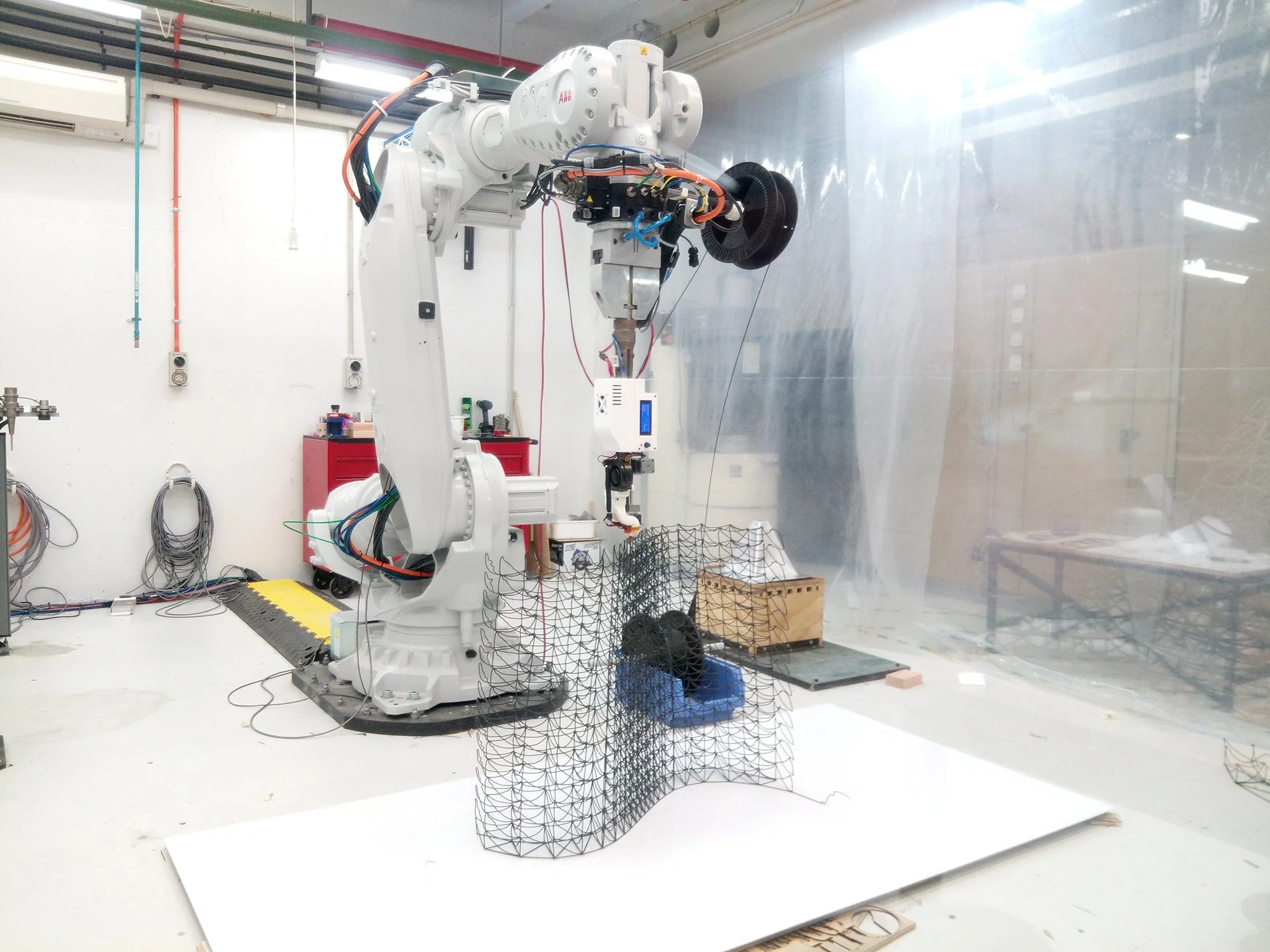
Communication Systems
In order to build a freeform printing system that operates synchronously between the robot and the extruder, we first needed to upgrade the robot with a set of industrial 24V signals and power transmission that the extruder can integrate with.
To achieve this we used an Arduino-based industrial PLC that mounts on the end of the robot, and to test this new system and how we program it I made a programmable LED to can be controlled by the robot. Using long-exposure photography we can see what the robot is doing along the programmed toolpaths, and could also use this to make light previews of freeform prints and experiment with some fun light painting
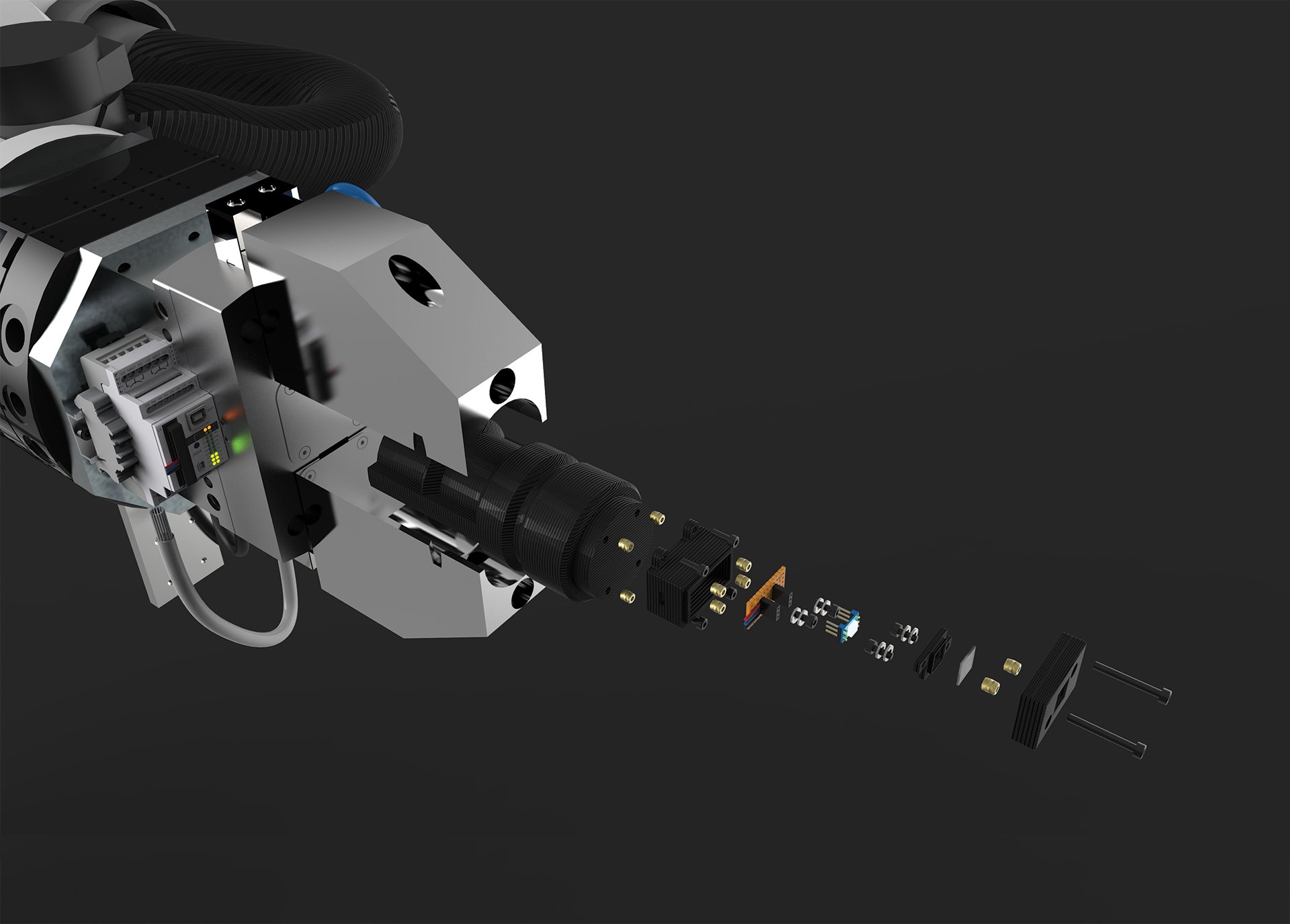

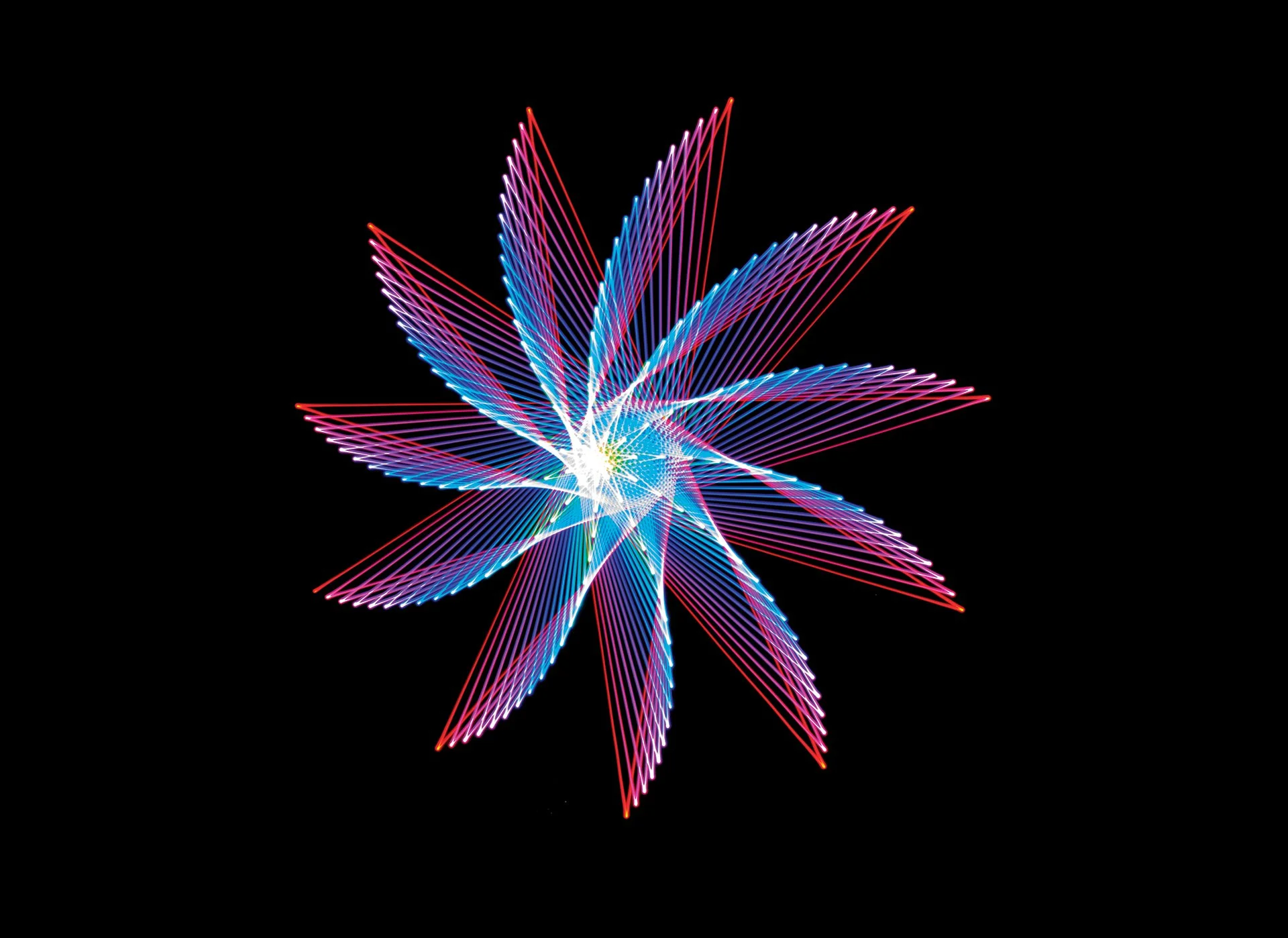
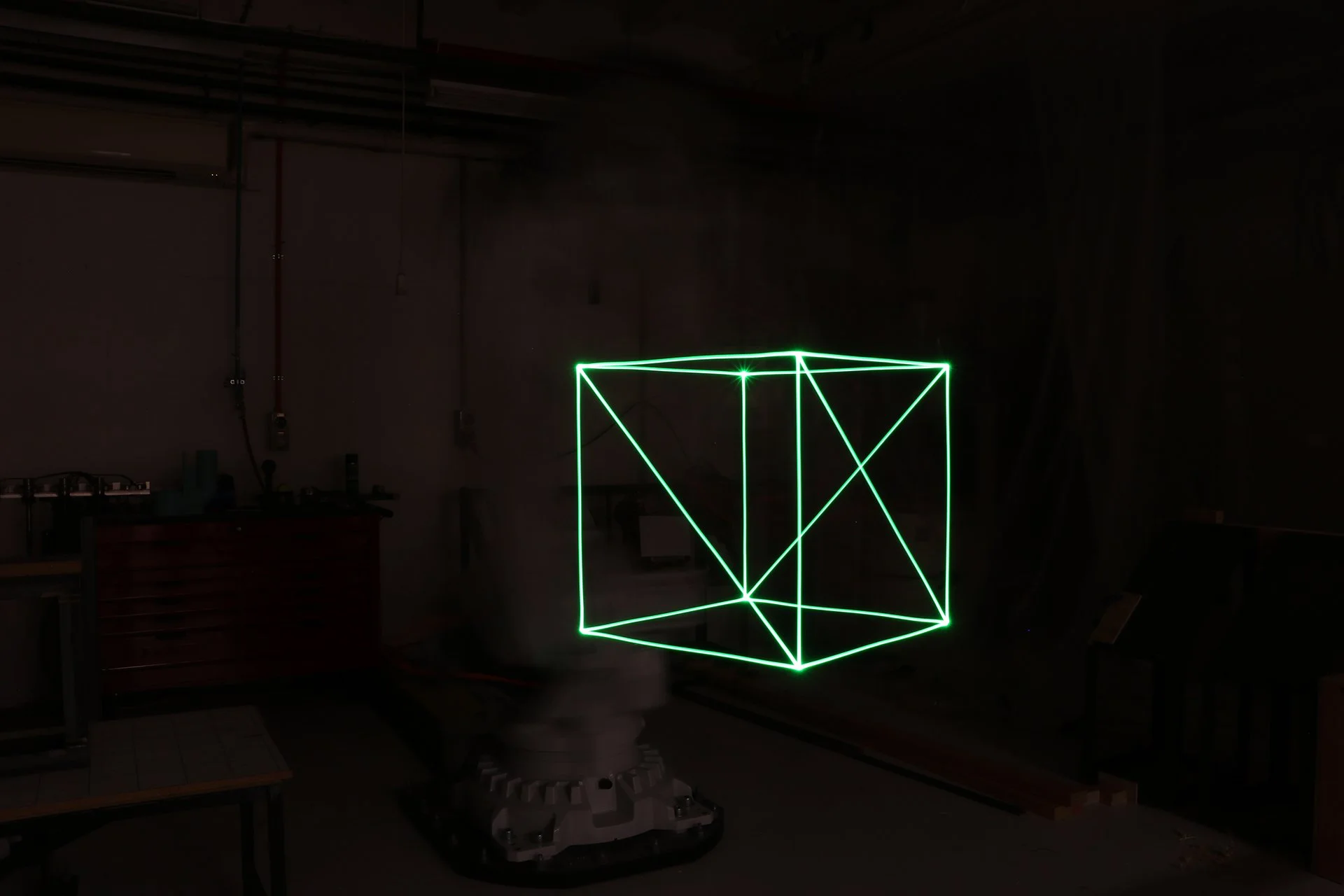
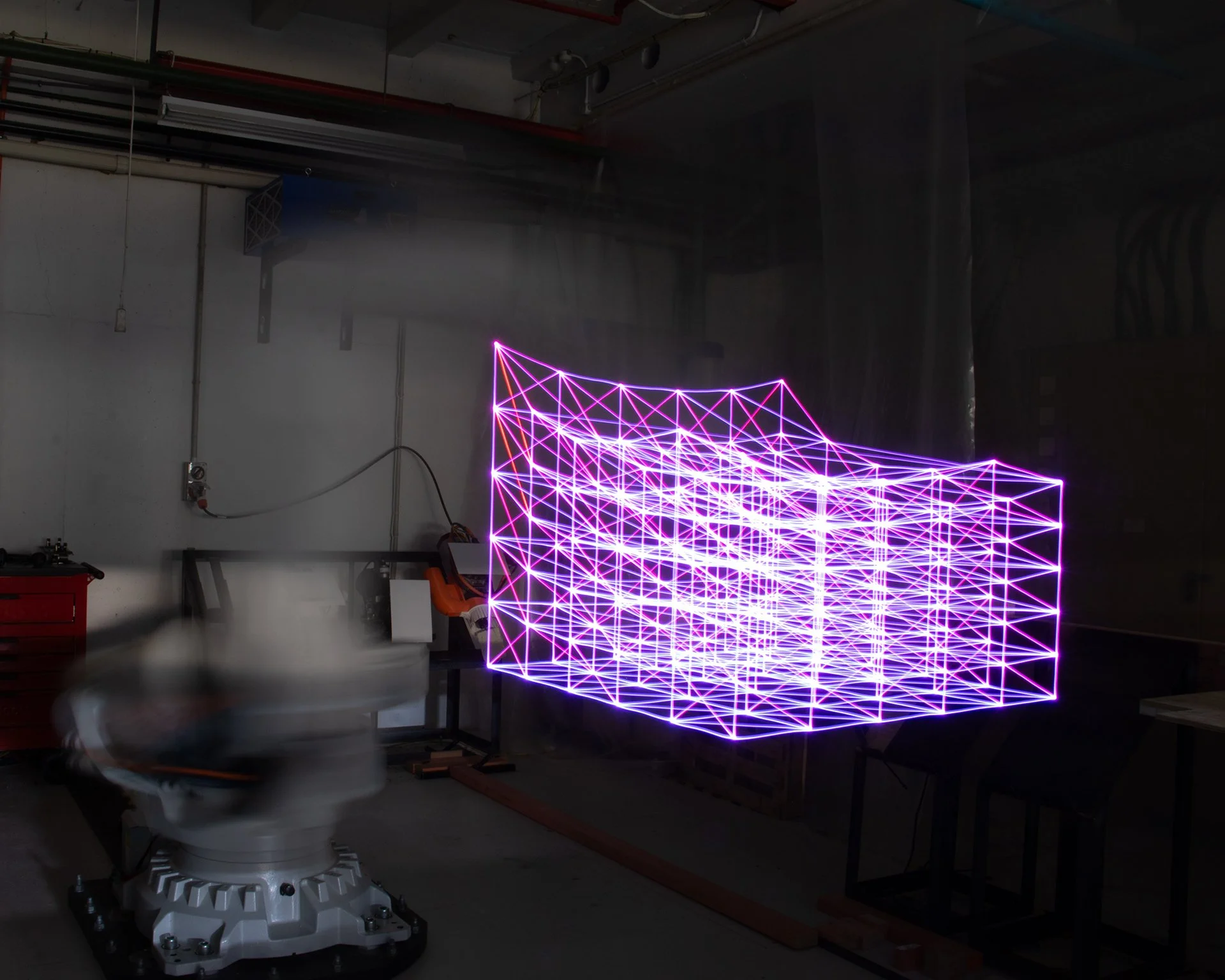

Second Extruder
The second sustem I design fully integrated into the the ABB robotic system using a new tool changer system with power systems and an array of analog and digital I/Os. All of the printing variables such as temperature and extrusion rate could be controlled by the robotic system, and extrusion could be aligned with movement and cooling which allowed us to make travel moves, split the models into sections, and vary cooling to prevent material deflection.
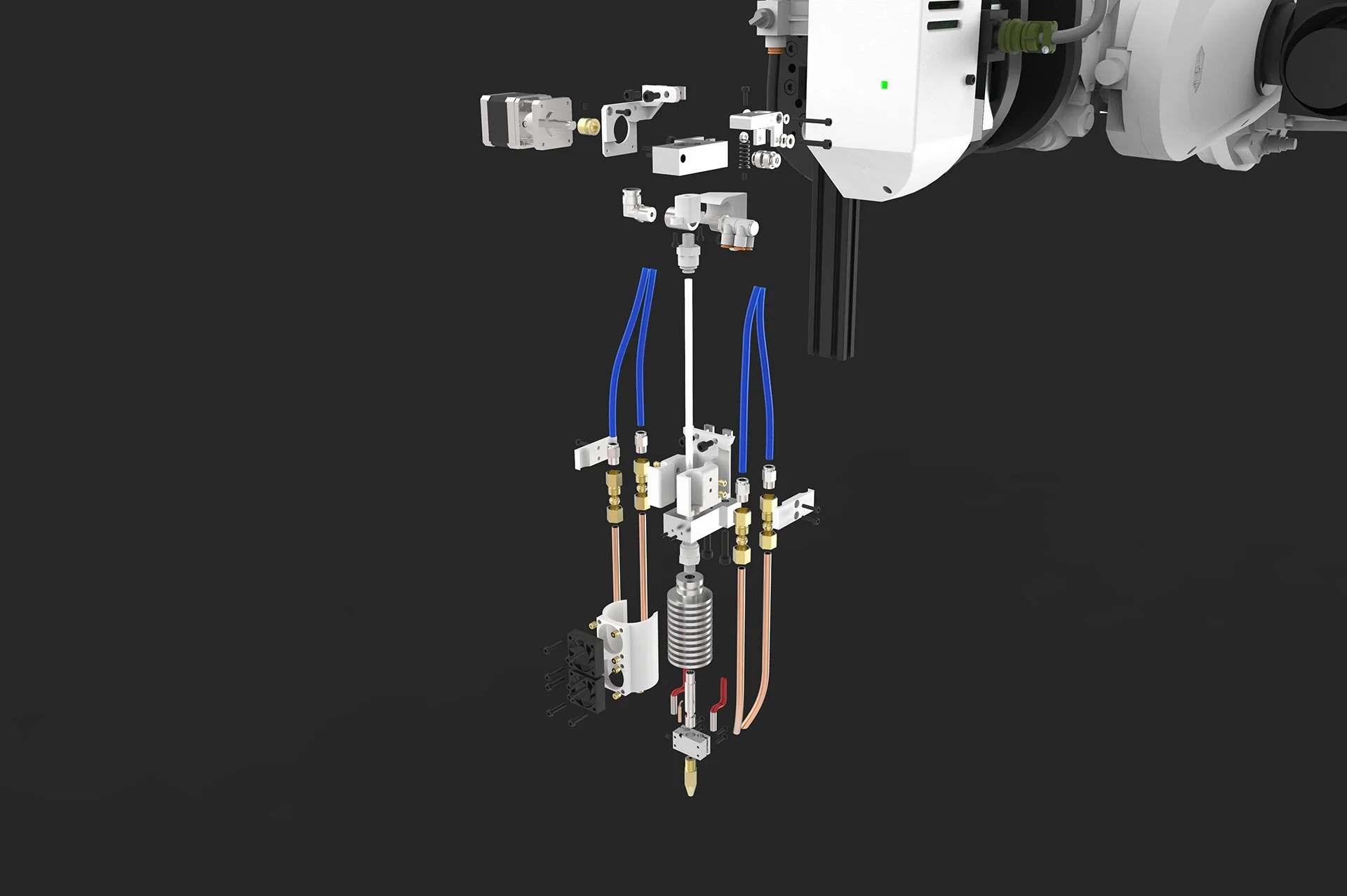
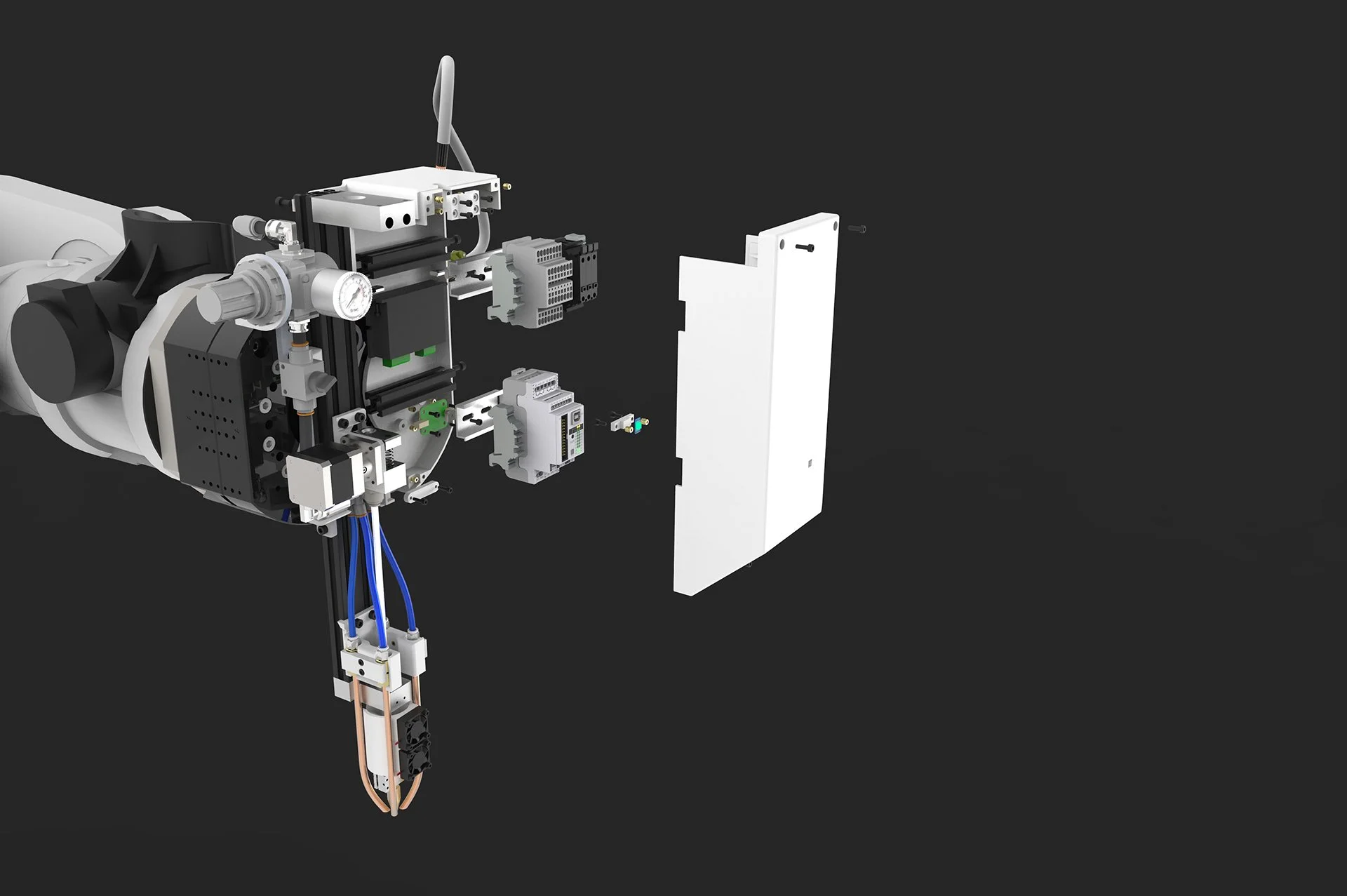

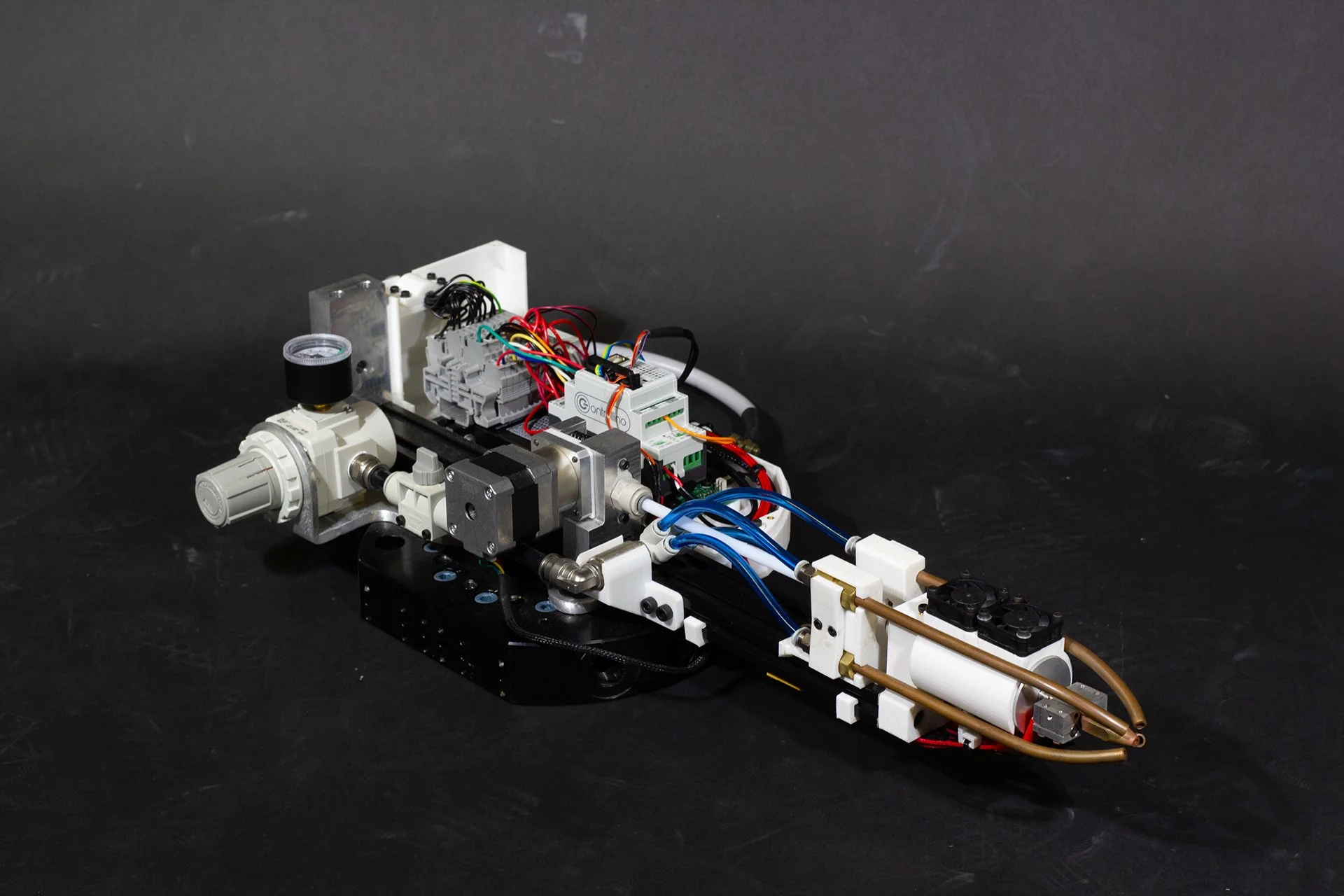

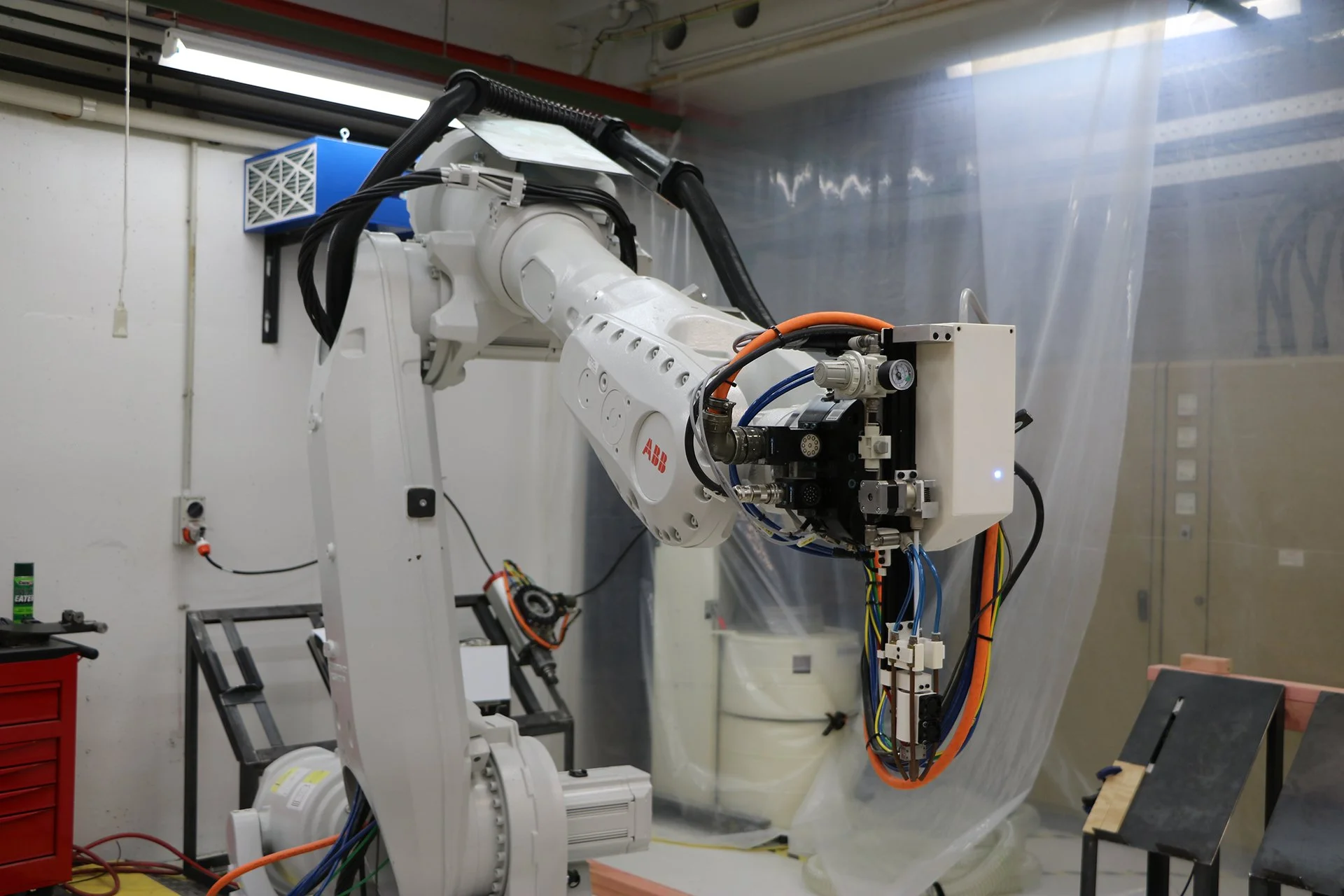
Read the full thesis
To view or download this thesis, visit:
https://openaccess.wgtn.ac.nz/articles/thesis/Robotic_Spatial_Printing_For_Designers/17135153?file=31687013